Tooling Design
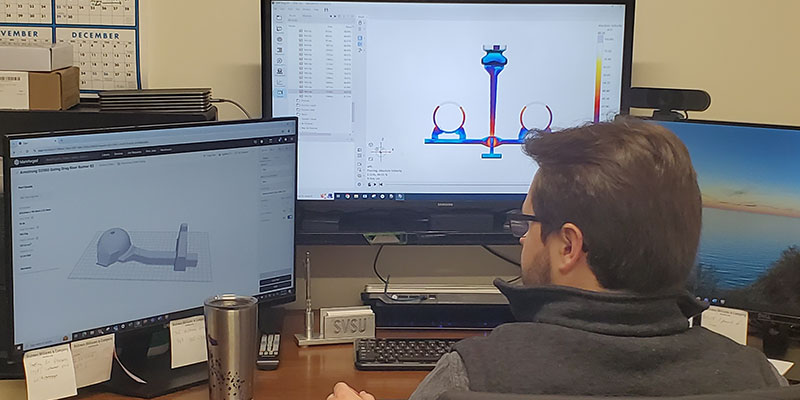
Tooling Design
Comprehensive Pattern Shop for Precision and Efficiency
Benefits of Our Engineering Resources Are As Follows:
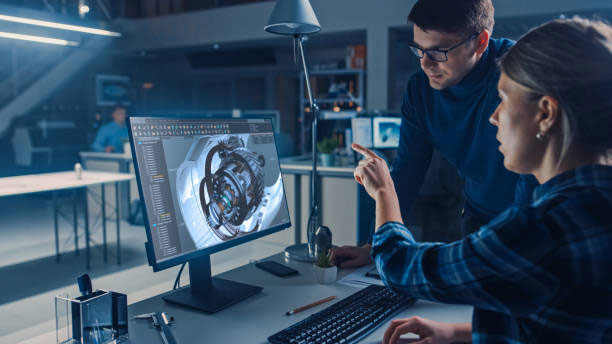
Advanced CAD/CAM Expertise
Our dedicated team of tooling designers uses the latest CAD/CAM technology and 3D modeling techniques to:
- Optimize Gating and Risering: Ensure proper metal flow and minimal scrap for consistent quality
- Enhance Mold Stability: Improve casting integrity by identifying and preventing potential weak points
- Minimize Material Waste: Streamline the design to reduce excess weight and enhance casting efficiency
This data-driven approach to tooling design ensures every mold or die is built to precise specifications, resulting in uniform casting quality across every batch.
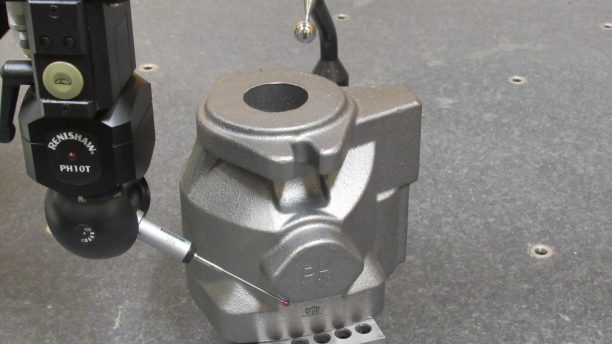
Collaborative Engineering Approach
From initial concept through final production, our engineers and tooling specialists work closely with clients to:
- Identify Key Requirements: Define exact dimensional, mechanical, and performance criteria
- Tailor Designs for Manufacturability: Adjust tooling features to optimize castability and reduce cycle times
- Accelerate Time-to-Market: Employ agile design processes that shorten development timelines
By involving our customers at every step, we deliver tooling solutions that meet or exceed project objectives while staying on budget and on schedule.
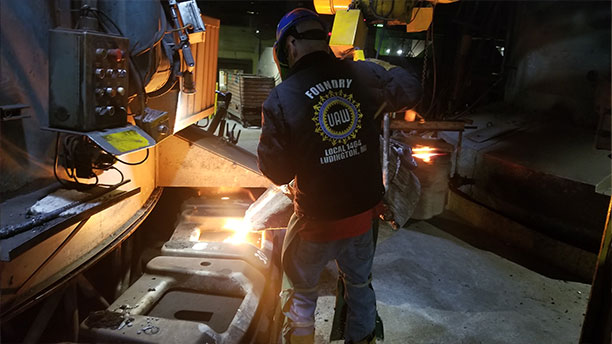
Versatile Materials & Techniques
Whether you’re casting gray iron, ductile iron, or other alloys, our team has the expertise to design and fabricate tooling that can handle:
- Moderate to High-Volume Production: Seamless transitions between matchplate molding and vertical molding
- Complex Geometries: Intricate part features, thin walls, and tight tolerances
- Specialized Applications: Components requiring annealing, advanced surface finishing, or machining
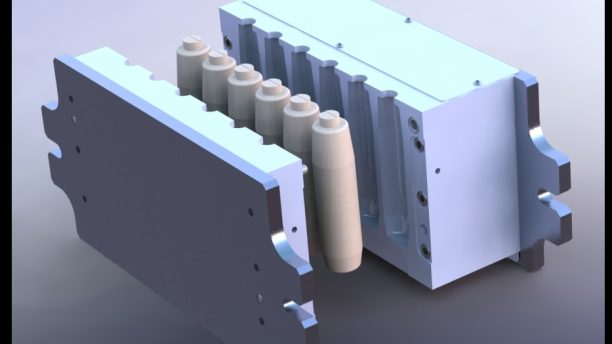
Quality Assurance & Validation
At Great Lakes Castings, we believe that tooling design success hinges on robust quality assurance. Before tooling is released to production, we run a series of dimensional checks and simulation validations:
- Dimensional Layout Reviews: Ensure critical tolerances and alignments are maintained
- Casting Simulations: Utilizing MAGMA, we predict metal flow, thermal gradients, and potential hot spots
- Prototype Testing: Validate real-world performance and address any design refinements early
- 3D Scanning: No pattern? No problem! We can scan your part and rebuild it to spec.
These pre-production checks reduce trial-and-error, save time, and lower costs, guaranteeing each tool is ready for efficient casting from day one.
Seamless Integration with Other Services
Our tooling design services integrate seamlessly with our precision casting, and finishing operations. This end-to-end approach ensures consistent communication and quality standards across all stages of gray and ductile iron casting—from initial design to final product delivery.
We accept inherited tooling and can cast to your specific needs.