Tooling Expertise
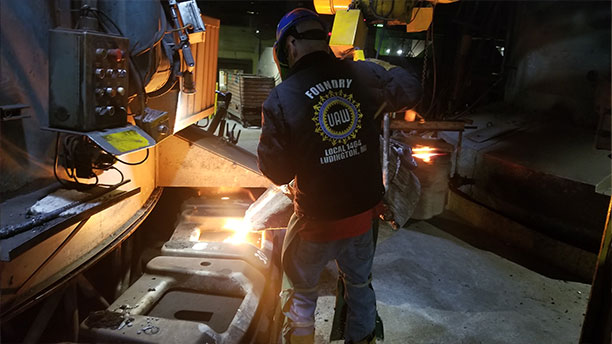
Our Approach to Pattern Making
We partner with trusted external suppliers to ensure top-quality patterns for your casting needs.
Flexible Production Capabilities
From low-volume prototypes to high-volume production runs, we adapt our processes to match your specific casting requirements.
Quick Turnaround Times
Our integrated operations eliminate the need for multiple outsourcing steps, enabling us to shorten lead times and maintain consistent quality throughout the process.
Expert Collaboration
Our pattern makers work closely with tooling engineers and foundry specialists to ensure seamless integration across casting, machining, and finishing stages.
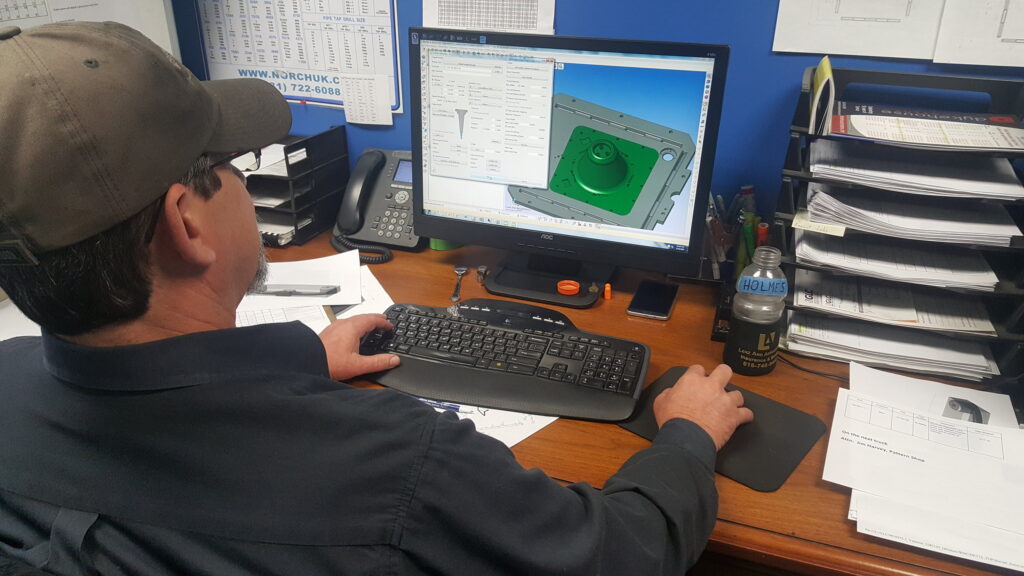
Ensuring Optimum Castibility
We analyze:
Mold Filling and Solidification
We ensure the pattern design supports efficient gating, proper metal flow, and optimum riser placement.
Ventilation and Cooling
Strategic venting solutions minimize defects like porosity or hot tears, resulting in reliable final castings.
Dimensional Stability
Patterns must accommodate material shrinkage, ensuring that cast parts stay within tight tolerances.
This thorough design approach helps produce castings that consistently meet or exceed industry standards.
Quality Control and Testing
Before moving to production, we employ rigorous quality checks to verify every pattern:
Dimensional Layout Reviews: Confirm pattern accuracy against original design specifications.
Trial Runs and Prototyping: Identify potential improvements early, reducing rework and waste.
Regular Maintenance: Keep patterns in peak condition for long-term reliability and consistent casting performance.
By focusing on preventative checks, we help you avoid costly errors, shorten production cycles, and maintain on-time deliveries.
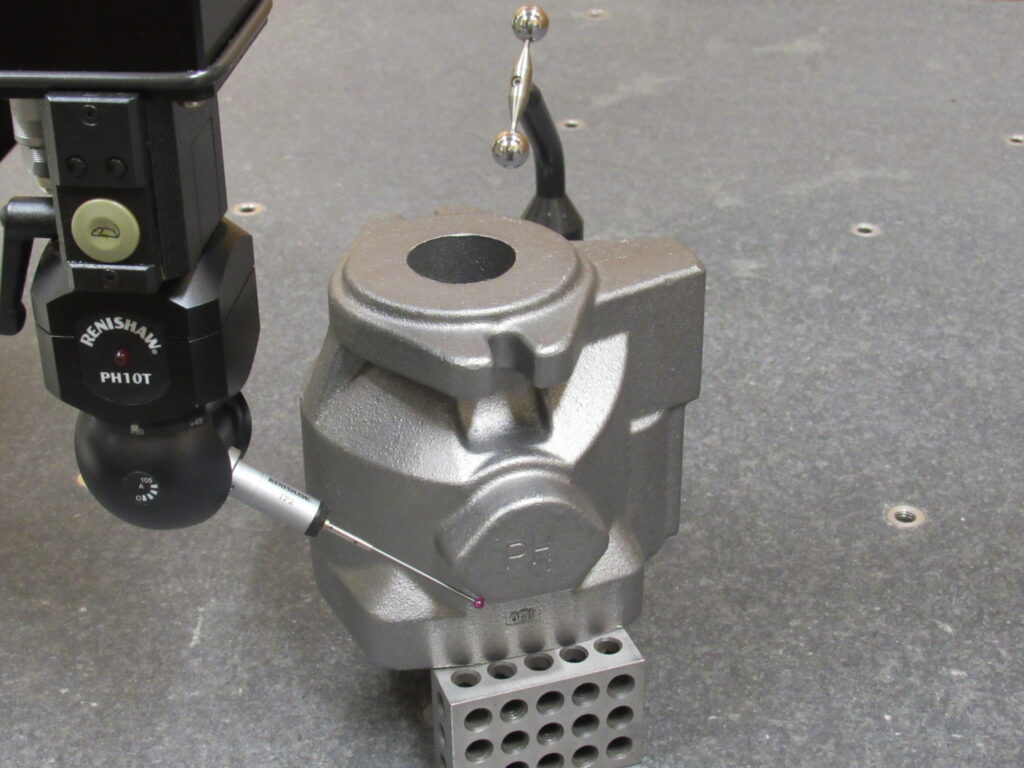